DTF Printing Explained | The Printer DTF Process
The printing industry has experienced rapid growth in recent times, with more and more organizations moving to DTF printers. But what is a DTF printer and why is it set to change the industry?
The use of Printer Direct-to-Film or Printer DTF allows you to embrace simplicity, convenience, and performance consistency with a wide range of colors. In addition, DTF printers are now reliable and cost-effective machines to own.
Let’s find out what DTF printing can do for you.
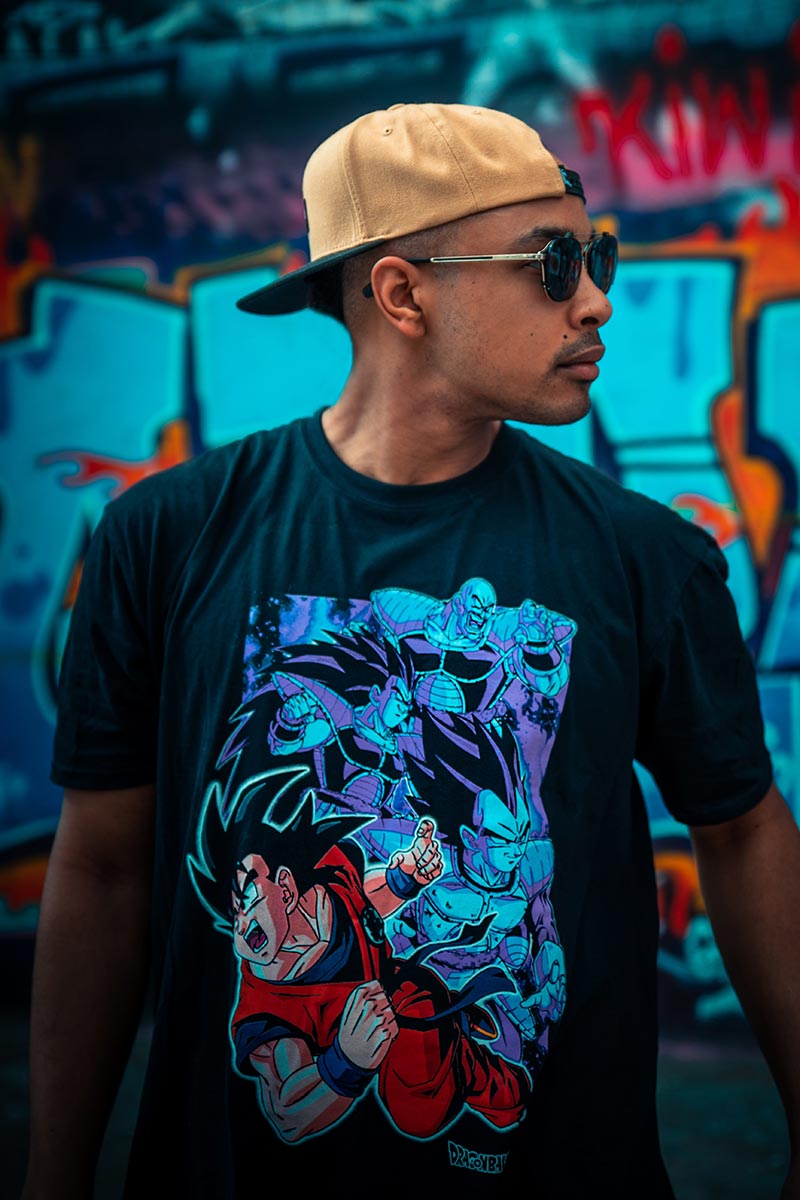
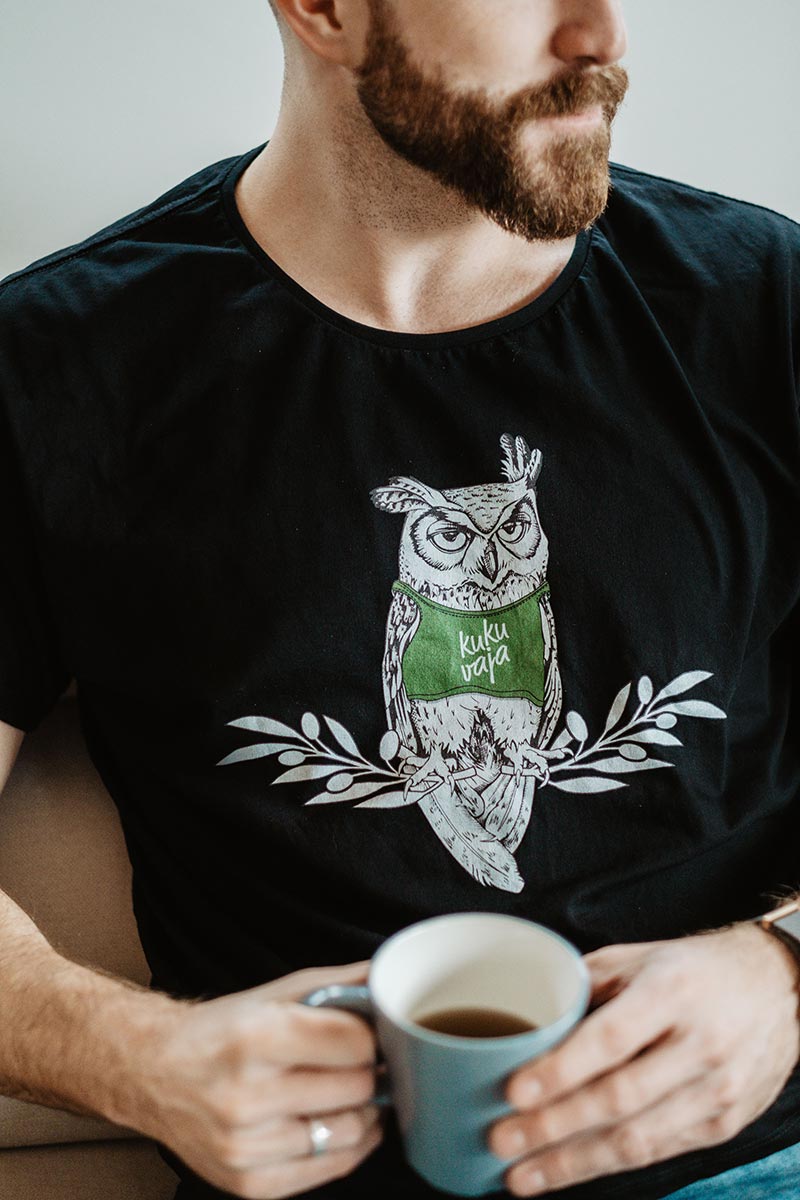
What is DTF Printing?
Direct-to-film or DTF printing is a process that transfers prints onto fabric or other substrates using a heat-press mechanism. Unlike the DTG method, which only works on cotton fabrics, the Printer DTF method can work on cotton and poly blends.
The freedom to use a wide array of production materials, the ability to recreate high-quality designs on large orders quickly, and the wash resistance and durability of the prints on apparel fabrics are just a few reasons why premium DTF is a great choice for many businesses.
What is a DTF Printer?
As the name suggests, a direct-to-film printer allows you to print a design on a film and transfer it directly to the intended surface, such as fabric. The key reason the printer DTF is gaining prominence is the freedom it gives you to print on almost any surface.
The DTF printer technology allows you to print easily on cotton, polyester, synthetic, or silk. DTF printers work on both dark and white fabric without needing to press on expensive A&B paper.
How Does a DTF Printer Work?
Implementing printer DTF in your printing business does not require a heavy investment. Whether you are new to the printing business or wish to adapt your DTF printing to expand your business, taking a closer look at these printers is worth your time.
DTF-modified printers typically come with multiple colored ink tanks. These tanks allow the printers the convenience of operating using CMYK settings. The DTF printer ink is specifically designed for use with this process.
Additionally, the DTF process eliminated the use of rollers that previously caused the page to slide. This rectifies the appearance of any linings on your white-layer prints. So, if you are looking for a printing technology that creates flawless final designs of the image you wanted on the fabric, DTF is the choice.
Direct-to-Film Printer Films
What is a DTF transfer made from that makes it different from transfers in screen printing? A DTF printer uses PET films (also known as DTF transfer films) with a thickness of approximately 0.75mm. This thickness gives them better transferring characteristics.
You can find them as cut sheets for small-scale use or as rolls for large commercial setups. PET films are classified based on temperature: cold-peel type films and hot-peel type films.
Software for DTF Printers
Software is an integral part of DTF printers. This is because software influences the color performance, print characteristics of the inks, and final print performance. For DTF printing, you will need specialized RIP software to handle your white and CMYK colors.
Having the right software is essential because it governs color profiling, drop sizes, ink levels, and several other critical factors contributing to print quality.
Hot-Melt Adhesive Powder
The direct-to-film printing powder is a white granular product and works as an adhesive material. This helps bind the colored pigments in your printer to the surface you are printing on. Several grades of this STF hot-melt are specified in microns.
DTF Printer Inks
The inks used in DTF printing are unique pigments designed in Cyan, Yellow, Magenta, White, and Black. The white ink forms the foundation of your print, while the colored pigment prints the design on the film.
Automatic Powder Shaker
This Direct-to-film printer component is commonly used in commercial applications. The shaker helps the DTF printer apply the powder in an even fashion while removing excess powder.
Curing Oven
This is a small industrial oven that melts the printer’s hot melt powder, which then goes on the transfer film. You can also use a heat press machine to carry out this function. However, it would help if you used the heat press machine in a no-contact mode.
Heat Press Machine
This piece of equipment helps transfer the printed images on your film onto the desired surface or fabric. You can also use this machine to melt powder on your DTF film.
Pros and Cons of DTF Printing
So, is it worth investing in a DTF printer? First, let’s examine its advantages and potential drawbacks
- PROS
- It does not require any pretreatment
- You can use it on almost any material or fabric
- When you touch the material it is printed on, it will still have a slight hand feel. After the printing, the fabric will exhibit excellent wash resistance.
- The process is less tedious and quicker than other printing methods, such as DTG.
- CONS
- The printed area is slightly more noticeable than subliminal printing
- The color vibrancy is somewhat lower than in sublimation printing
Why DTF Printers
DTF printers and the specialty ink they use can produce premium-quality printing. They can also help bring out the brightness and delicacy of the color tones in both dark and light fabrics.
The textile industry predicts that demand for DTF printers will grow steadily in years to come. The industry believes that more and more companies will start to use the DTF printing technology thanks to the many benefits it offers. So, if you’re a textile or t-shirt company that wants to produce printed fabric efficiently and economically, a DTF printer is the way forward.
It’s clear that DTF printers can practically lift most of the restrictions inherent in the traditional commercial printing processes. Moreover, since the process doesn’t require treatment in most cases, DTF printers offer you savings on overall printing costs. This can provide your organization with higher profit margins.
Find more information about the ColDesi DTF Printers here.