High Volume Digital Printing | Better Workflow with a Barcode Reader
Digital Printing shops that do, or WANT to do, higher volume work are always looking for 2 things:
#1: Better Workflow – that’s more efficiency, less confusion and better turn around time for customer orders.
#2: Reduced labor cost – other than feeding your D2 printer ink or toner and paying your rent, there’s no bigger expense in most businesses that labor.
If you are looking for ways to improve workflow while also reducing labor costs in your printing operation [which you ARE, of course] then adding a barcode scanner to your operation could be a silver bullet.
It is especially important if you have more than one operator of your printing equipment – whether it be D2 [direct to garment printing], UV or even white toner based lasers like the Digital HeatFX. Because it minimizes the software knowledge required by your operator.
And that can help to reduce both errors and labor costs.
If you are running multiple machines you can have one graphics person preparing all of your output and let the machine operators simply point, shoot, load, print and repeat!

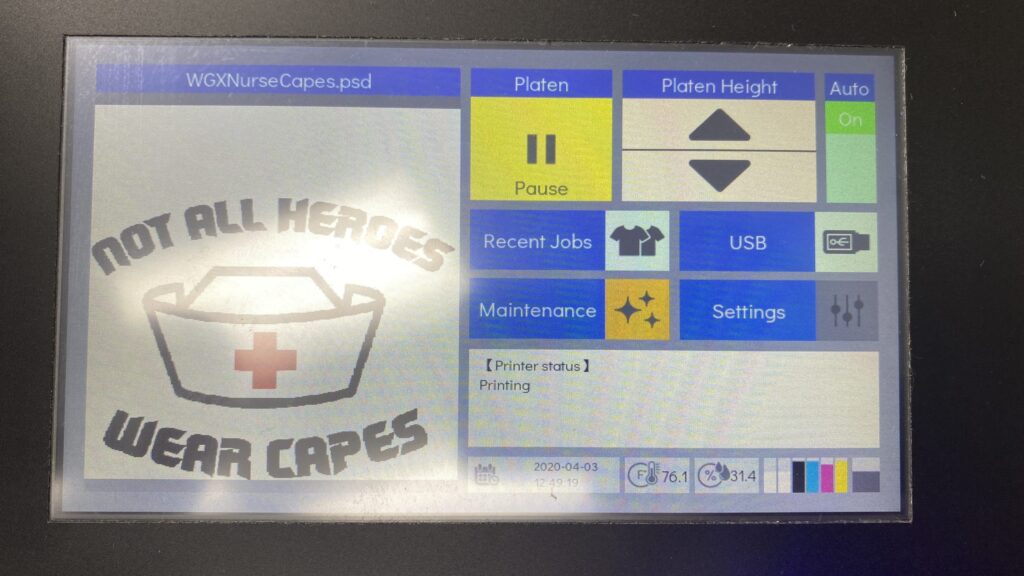
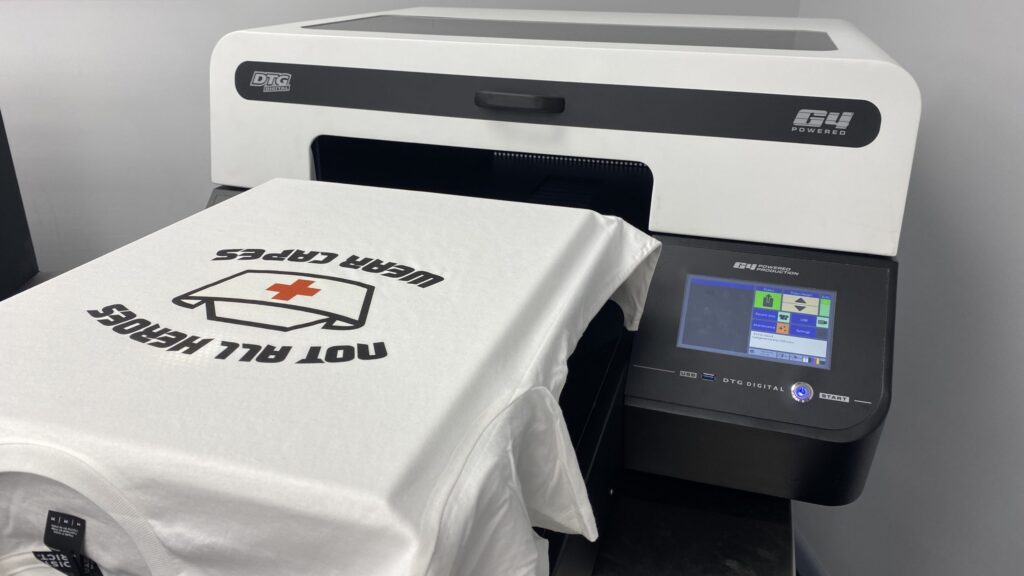
How a Barcode Reader can Improve Workflow
Let’s look at a couple scenarios where using a barcode scanner could be used. In this case we will use the example of a direct to garment printing operation.
Online or on demand print operation selling their own designs – this would be a company that has a “catalog” of designs that they have created and produce on demand instead of keeping a heavy inventory of preprinted shirts.
This sort of operation can easily reduce their inventory by 80-90% or more by becoming “just in time” printers. The workflow could be setup in a couple of ways.
Barcode Reader Implementation Option 1:
Printed catalog for each workstation
The operator would receive an order sheet with:
- The name for a specific job
- Color and size of the shirt to print
- Quantity
Upon receiving the order the operator simply scans the barcode in the catalog.
That loads the design in the proper hot folder, RIPs it and sends the design to the printer.
The operator then would load a pretreated shirt onto the printer and processes the order.
If there are multiples of the same job to be repeated the operator simply reprints the job from the memory of the printer (if it has one like the DTG G4) or re-scans the barcode to RIP and print the design again.
Operations like this keep a master database of their artwork in one location on their network and add to them each time a new design is created and also update their printed catalog.
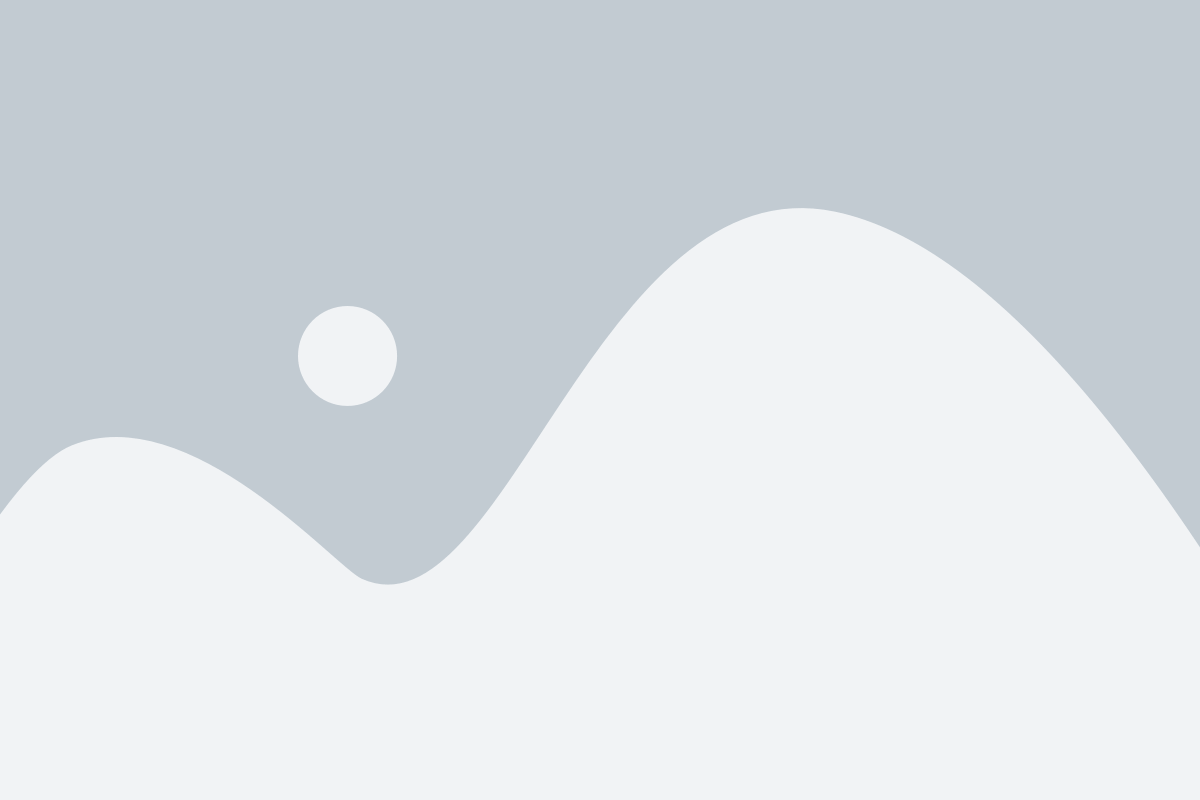
Advantages of this Method
The work order generation software does not have to have to be able to generate barcodes, can be done electronically by email since no barcode is to be scanned from the work order, can be easily automated since there are a finite number of images to work from.
Disadvantages of this Method
Generally this would be for sending work orders to specific users on specific machines, not as efficient as having operators pick up orders as they are freed up, anytime that new designs are added a new catalog needs to be printed for each work station, not beneficial for operations where a lot of custom work is done.
Barcode Reader Option 2:
Printed catalog for each workstation
The operator would receive an order sheet with:
- -The name for a specific job
- -Color and size of the shirt to print
- -Quantity
Upon receiving the order the operator simply scans the barcode in the catalog.
That loads the design in the proper hot folder, RIPs it and sends the design to the printer.
The operator then would load a pretreated shirt onto the printer and processes the order.
If there are multiples of the same job to be repeated the operator simply reprints the job from the memory of the printer (if it has one like the DTG G4) or re-scans the barcode to RIP and print the design again.
Operations like this keep a master database of their artwork in one location on their network and add to them each time a new design is created and also update their printed catalog.
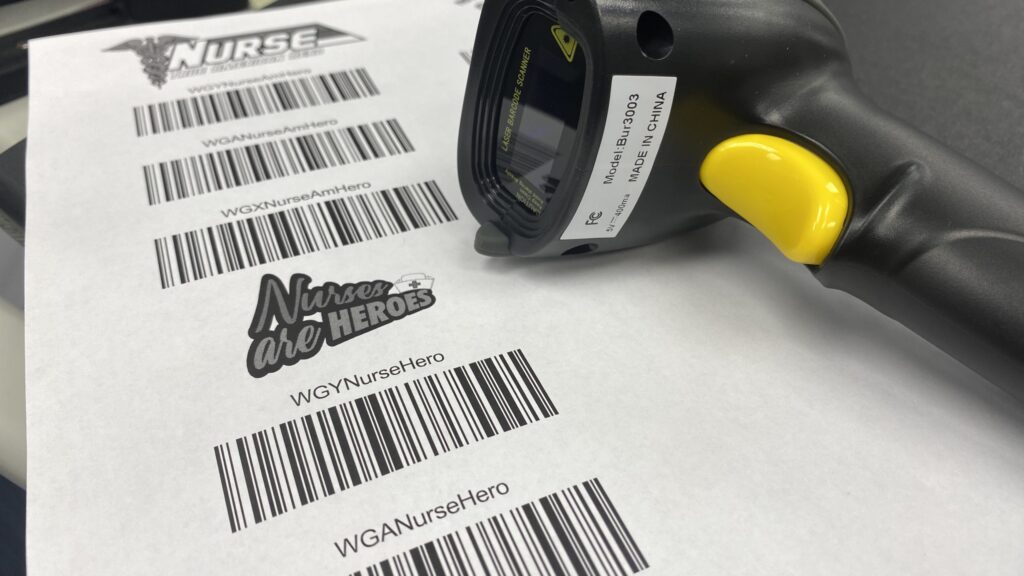

Advantages of this Method
Most efficient way to handle custom and short run orders, operators not overwhelmed by an inbox full of orders.
They simply finish an order and pick up the next one off the printer. It allows for an efficient mix of stock and custom designs as each order is unique even if it is a stock design.
That’s because each work order is a unique printout there is little chance of two or more operators printing the same job or of an operator duplicating the order (especially if emailed work orders in previous method are not moved to a completed folder)
Disadvantages of this Method
A lot of paper used (at least one sheet per order), need for a work order printer in your print operation, logistics of strategically placing work order printer to maximize workflow, overkill for a stock design only, small catalog operation.
How to organize your shop using a barcode reader
As you can see there are some decisions to be made before you determine if a barcode system for your printing workflow is the best solution.
It certainly is if you have multiple printers, especially so if they are located in multiple locations (think of a multi-site business where customers may want to place orders for their locations in multiple cities where you have store fronts).
For many companies it allows you to reduced the required skill set of the printer operators allowing them to focus on becoming better at whet they do while relying on a more limited number of more skilled graphics employees to make sure that artwork is properly setup for printing.
More efficient operations, lower payroll expense, more specific job descriptions all result in a better, more profitable operation. And that is really what everyone wants.